Modular homes are becoming an increasingly popular option for those looking to build a new home. They offer a number of benefits, including affordability, faster move-in times, and the ability to customize your home to your exact specifications. However, one question that many people have when considering a modular home is whether or not they come with electrical and plumbing.
The answer to this question is yes, most modular homes come with the necessary electrical, plumbing, and HVAC required services. However, the necessary services may differ depending on different factors such as the modular home company, location, or climate. It’s important to do your research and make sure that the modular home you’re considering has all the necessary services that you need. In this article, we’ll take a closer look at modular homes and what you need to know about their electrical and plumbing systems.
Understanding Modular Homes
Modular homes are prefabricated homes that are built in a factory and then transported to the site where they will be assembled. These homes are built using modules, which are pre-built sections of the home that are then assembled on-site to create the final product.
Modular homes are becoming increasingly popular due to their affordability, speed of construction, and customization options. They are also known for their high-quality construction, energy efficiency, and durability.
One of the most common questions people have about modular homes is whether they come with electrical and plumbing. The answer is that most modular homes do come with the necessary electrical, plumbing, and HVAC required services. However, the necessary services may differ depending on different factors such as the modular home company, location, or climate.
It’s important to note that modular homes are not the same as manufactured homes. Manufactured homes are also prefabricated homes, but they are built to different standards and codes than modular homes. Modular homes are built to the same codes and standards as traditional stick-built homes, which means they are subject to the same inspections and regulations.
Clayton Built® homes are a popular type of modular home that are known for their high-quality construction and customization options. These homes are built using advanced construction techniques and materials, which means they are more energy-efficient and durable than traditional stick-built homes.
In conclusion, modular homes are a great option for those who are looking for an affordable, customizable, and high-quality home. Most modular homes come with the necessary electrical, plumbing, and HVAC required services, but it’s important to check with the modular home company to ensure that everything is included. With their many benefits, it’s no wonder that modular homes are becoming an increasingly popular choice for homeowners.
Modular Homes Vs Site-Built Homes
When it comes to choosing a home, buyers have a variety of options to consider. One of the most significant decisions is whether to purchase a modular home or a site-built home. Here are some key differences between the two:
Construction Process
Site-built homes are constructed on the property where they will be located, while modular homes are built in a factory and then transported to the site. Modular homes are constructed in sections, or modules, that are then assembled on site. This means that modular homes can be built more quickly than site-built homes, as the construction process is not affected by weather or other environmental factors.
Customization
Site-built homes offer more customization options than modular homes. Buyers can work with architects and builders to create a unique design that meets their specific needs and preferences. Modular homes, on the other hand, are built according to pre-designed plans, which limits the amount of customization that is possible.
Cost
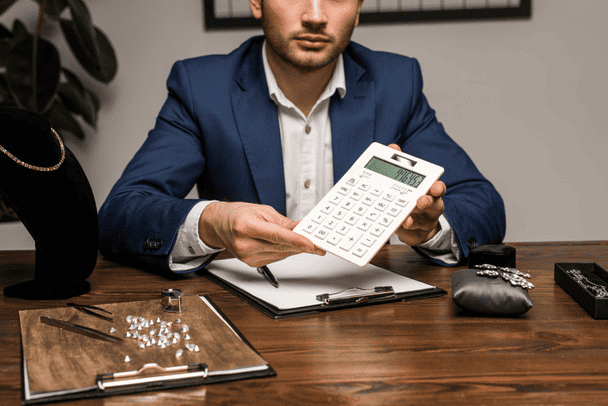
Modular homes are generally less expensive than site-built homes, as they can be built more quickly and with less waste. However, buyers should be aware that the cost of a modular home can vary depending on a variety of factors, including the size of the home, the materials used, and the location.
Resale Value
Site-built homes generally have a higher resale value than modular homes. This is because site-built homes are typically considered to be of higher quality and offer more customization options. However, the resale value of a modular home can be improved by ensuring that it is well-maintained and located in a desirable area.
In summary, both modular homes and site-built homes have their advantages and disadvantages. Buyers should carefully consider their options and choose the type of home that best meets their needs and preferences.
Construction of Modular Homes
Modular homes are built in a controlled factory setting, with each module fully finished, including painted walls, flooring, and kitchen cabinets. The construction process enforces the need to design all the installations, including electrical, plumbing, and HVAC, together with the home design. As a result, modular homes come with electrical and plumbing systems installed.
The factory setting provides a controlled environment for construction, ensuring consistency and quality of materials. Modular homes are made with the same materials as traditional site-built homes, including wood, concrete, and steel. The materials used are subject to the same building codes and standards as site-built homes.
The floor plan of a modular home is designed to fit the specific needs and preferences of the homeowner. The floor plan is created with the help of computer-aided design (CAD) software, which allows for customization and flexibility in design.
Once the main modules of a new home are constructed, complete with attached walls, floor, ceiling, wiring, plumbing, and interior fixtures, they are transported to the homeowner’s chosen lot and placed on a permanent foundation. The assembly of the modules on-site is done by a crew of trained professionals, ensuring the structural integrity of the home.
The flooring system of a modular home is designed to be strong and durable, with options including vinyl, laminate, and carpeting. Before the floor covering finishes off a home’s floor, holes are cut out for plumbing and electric, and PEX plumbing is installed.
In conclusion, modular homes are constructed in a factory setting, with each module fully finished and designed to fit the specific needs and preferences of the homeowner. The construction process enforces the need to design all the installations, including electrical and plumbing, together with the home design. The materials used are subject to the same building codes and standards as site-built homes, and the assembly of the modules on-site is done by a crew of trained professionals.
Electrical Systems in Modular Homes
Modular homes come with electrical systems that are installed during the manufacturing process. The electrical systems in modular homes are similar to those in traditional site-built homes, but there are some differences to consider.
Electrical Wiring
Modular homes are built with electrical wiring that is installed in the factory. The wiring is installed according to the National Electrical Code (NEC) and is inspected and tested before the home is shipped to the site. The NEC is a set of guidelines that governs the installation of electrical wiring in buildings. It is important to ensure that the electrical wiring in your modular home meets the NEC code requirements.
Circuit Breakers
Modular homes are equipped with circuit breakers that are designed to protect the electrical system from overload. Circuit breakers are installed in the electrical panel and are designed to trip when there is an overload of electricity. This helps to prevent electrical fires and other hazards.
Appliances
Modular homes come with appliances that are designed to work with the electrical system in the home. It is important to ensure that the appliances you choose are compatible with the electrical system in your modular home. If you are unsure, consult with a professional electrician.
Testing
Modular homes undergo rigorous testing before they are shipped to the site. The electrical system is tested to ensure that it is functioning properly and meets the NEC code requirements. It is important to ensure that the electrical system in your modular home is tested and inspected by a professional electrician before you move in.
In conclusion, modular homes come with electrical systems that are installed during the manufacturing process. The electrical systems in modular homes are similar to those in traditional site-built homes, but there are some differences to consider. It is important to ensure that the electrical system in your modular home meets the NEC code requirements and is tested and inspected by a professional electrician.
Plumbing in Modular Homes
Modular homes come with plumbing systems that are similar to those found in traditional site-built homes. However, the location of the plumbing pipes and fixtures may differ due to the unique construction of modular homes.
The plumbing system in a modular home typically includes supply lines, drain lines, and a septic system. The supply lines carry water to each fixture, while the drain lines remove wastewater from the home. Modular homes may use either PVC or copper plumbing pipes, depending on the builder’s preference.
The water supply lines in a modular home are typically located under the home’s flooring or in the walls. The fittings used in the plumbing system are also similar to those found in traditional homes. However, it is important to note that the location of the plumbing pipes may vary depending on the specific design of the home.
In terms of the septic system, modular homes can be connected to either a public sewer system or a private septic system. If the home is connected to a private septic system, the drain lines will be connected to a septic tank, which will then be pumped out periodically.
Overall, modular homes come equipped with a plumbing system that is similar to those found in traditional site-built homes. While the location of the plumbing pipes and fixtures may differ, the materials and fittings used in the plumbing system are similar. It is important to note that the specific plumbing system in a modular home may vary depending on the builder’s preferences and the location of the home.
HVAC and Insulation in Modular Homes
Modular homes come with the necessary HVAC systems required for heating, ventilation, and air conditioning. However, the type of HVAC system may differ depending on the modular home company, location, or climate.
HVAC Systems in Modular Homes
Most modular homes come with an HVAC system that includes a furnace, air conditioner, and ductwork. The furnace is responsible for heating the home, while the air conditioner cools it down. The ductwork distributes heated or cooled air throughout the home.
The HVAC system in a modular home is typically installed by a licensed HVAC contractor. The contractor will ensure that the system is properly sized for the home and meets local building codes. The installation process may include running ductwork through the walls and floors of the home.
Insulation in Modular Homes
Insulation is an important aspect of any home, including modular homes. It helps regulate the temperature inside the home and can reduce energy costs. Most modular homes come with insulation in the walls, floors, and roof.
The standard insulation package for modular homes is R-21 in the exterior walls and R-38 in the roof. However, homeowners can upgrade the roof insulation to R-45 for a minimal charge depending on the manufacturer.
There are several methods used to add roof insulation to the existing cavity, such as drilling and tube blowing from the inside or top, and rolling back the roof and blowing into the now open cavity. Some installers prefer to use roof caps for insulating instead of filling the existing cavity.
HVAC Ductwork in Modular Homes
Ductwork in pre-assembled housing modules can be a challenge, which means some modular homes are going to come with electric baseboard heating as the standard. However, most modern modular homes come with ductwork that is installed on-site during the final assembly process.
The ductwork is typically installed by a licensed HVAC contractor. The contractor will ensure that the ductwork is properly sized for the home and meets local building codes. The installation process may include running ductwork through the walls and floors of the home.
In conclusion, modular homes come with the necessary HVAC systems required for heating, ventilation, and air conditioning. The type of HVAC system may differ depending on the modular home company, location, or climate. Insulation is also an important aspect of any home, including modular homes. It helps regulate the temperature inside the home and can reduce energy costs. The ductwork in pre-assembled housing modules can be a challenge, but most modern modular homes come with ductwork that is installed on-site during the final assembly process.
Utility Room and Foundations
Modular homes come with pre-installed electrical and plumbing components. This means that the utility room is already in place when the home arrives on-site. The utility room is where the home’s electrical and plumbing systems are connected to the main electrical and plumbing systems of the property.
The foundation of a modular home is also an important consideration. Modular homes need space under the home for electrical, heating and cooling, and plumbing connections. Therefore, the foundation type must include space between the subfloor and the ground, and the home cannot be built on a slab foundation. Common types of foundations for modular homes include:
- Crawlspace foundation: This type of foundation is a raised foundation that creates a space between the ground and the subfloor of the home. It provides easy access to the home’s electrical and plumbing systems and also helps to prevent moisture damage.
- Basement foundation: A basement foundation is a type of foundation that includes a basement space under the home. This type of foundation is ideal for homeowners who need extra storage space or want to create additional living space.
- Pier and beam foundation: This type of foundation consists of piers that support the weight of the home. The piers are placed on top of a concrete footing and provide a space between the ground and the subfloor of the home.
It is important to choose the right foundation for your modular home based on your location, climate, and budget. Your modular home company can provide guidance on the best foundation type for your home.
Inspections and Local Codes
When it comes to the installation of modular homes, inspections are a crucial part of the process. After the home has been built and transported to the site, all hookups are completed and inspected. The final inspection is to ensure that the modular home meets codes for egress (exterior steps), smoke detectors, and other safety measures. The installation inspection is essential to ensure that the home is installed correctly and meets all necessary codes.
Local codes for plumbing may take precedence over HUD Code when it comes to the connection of the plumbing systems to site connections for septic and water supply. It is important to check with your local home consultant to see what codes your plumbing and septic will be built to. This is because different locations may have different requirements for plumbing and septic systems, and it is important to ensure that your modular home meets these requirements.
Modular homes are built to meet national standards, but local codes may differ depending on location or climate. Therefore, it is important to understand the local codes and requirements for the area where your modular home will be installed. It is recommended to work with a knowledgeable and experienced contractor who understands the local codes and can ensure that your modular home meets all necessary requirements.
In summary, inspections and local codes are crucial elements to consider when installing a modular home. It is important to ensure that your modular home meets all necessary codes and requirements for your location. Working with a knowledgeable contractor can help ensure that your modular home is installed correctly and meets all necessary safety measures.
Affordability of Modular Homes
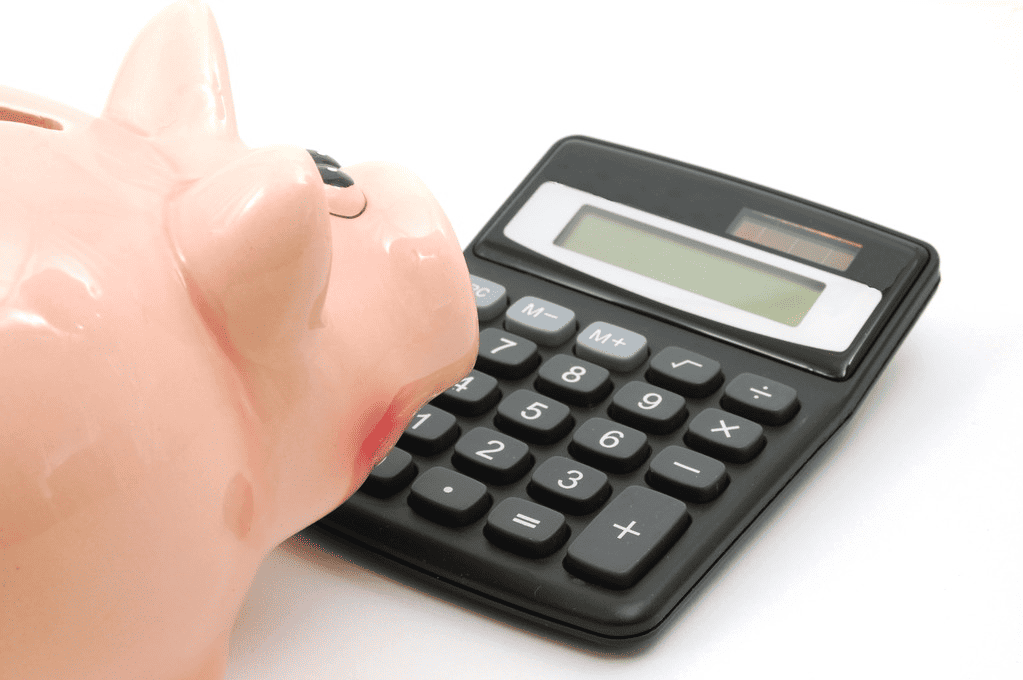
Modular homes are a popular option for those looking for affordable housing. Compared to traditional stick-built homes, modular homes are typically less expensive due to their factory construction process.
According to HomeGuide, the national average cost to install a modular home is $270,000, with prices ranging from $180,000 to $360,000. This cost includes foundation delivery and moving, set-up and installation, HVAC, electrical, and plumbing. However, the final cost may vary depending on the location, size, and customization options of the modular home.
One of the benefits of modular homes is their ability to be customized to fit various budgets and lifestyles. Modular home builders offer a range of floor plans and design options, allowing homeowners to choose a home that fits their needs and budget. Additionally, modular homes can be built with energy-efficient materials and appliances, which can save homeowners money on utility bills in the long run.
In summary, modular homes are an affordable housing option that can be customized to fit various budgets and lifestyles. Their factory construction process and energy-efficient features make them a cost-effective choice for those looking to own a home.
Damage and Repairs
Modular homes are built to withstand transportation and installation, but sometimes damage can occur during shipping or installation. If you notice any damage to your home, it’s important to document it and report it to the manufacturer and your contractor immediately.
Common types of damage to modular homes include:
- Dents or scratches on exterior siding or roofing
- Cracks in drywall or flooring
- Broken windows or doors
- Damaged plumbing or electrical systems
Fortunately, most repairs to modular homes are easy to make. The modules already come with plumbing and wiring installed, but they must be connected to each other. Your contractor will have to hire electricians, plumbers, and other specialists to make sure that the utilities are properly connected throughout the house.
If you need to replace outlets or switches, it’s important to make sure that you use the right type for your modular home. Modular homes require specialized outlets and switches that are designed for use in a factory-built home. Your contractor or electrician can help you choose the right products and install them correctly.
In general, modular homes are easy to repair and maintain. Because the homes are built in a factory, the construction process is highly controlled, which means that the quality of the materials and workmanship is consistent. This makes it easier to find replacement parts and to complete repairs quickly and efficiently.